GRAIN BIN BREAKTHROUGHS
BY MELANIE EPP • LEAD PHOTO COURTESY OF ADAPTIVE AGRICULTURE SOLUTIONS
Harvest is without a doubt the most hectic season, especially on big farms, where sheer volume compounds grain handling problems. Though workload increases with farm size, the time window to complete harvest does not. Setbacks such as labour shortage, harvest surge and inclement weather can be a major source of stress on farms of all sizes. New grain bin technology aims to alleviate such harvest pressures.
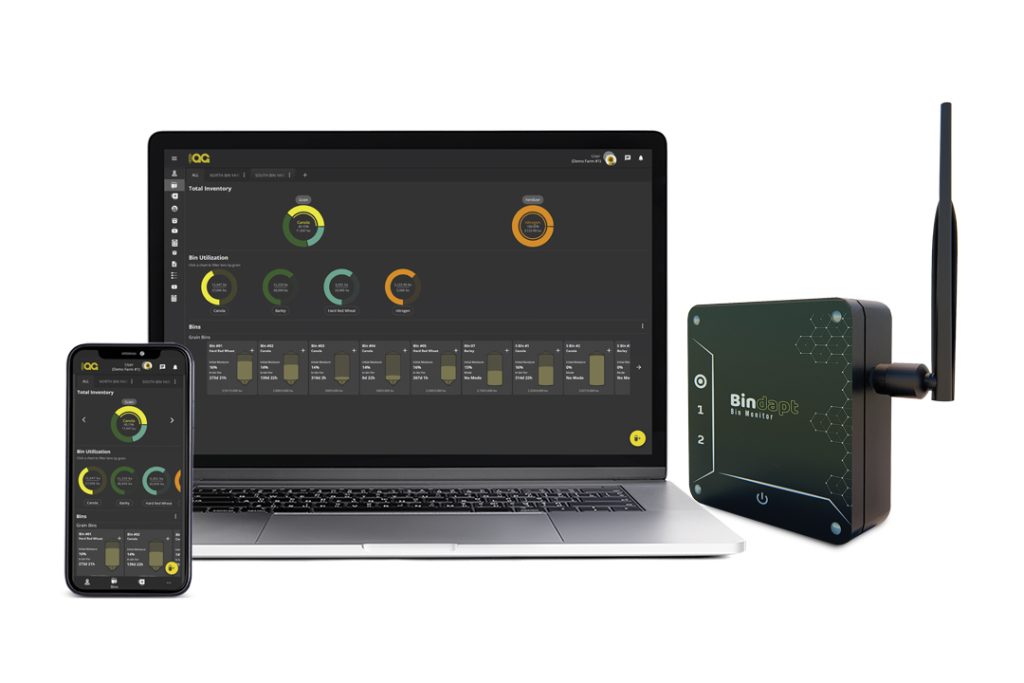
MAKE MINE A SMART BIN
Adaptive Agriculture Solutions of Saskatoon, SK, is best known for Bindapt, its automated in-bin drying system that consists of a thermostat controller and fan adapter plates paired with a heater. Powered by diesel, propane or natural gas, the heater moves warm, dry air through the grain column. The company has now added sensor technology to the system. Two versions, Bindapt+ and Bindapt+ Pro, allow farmers to turn their aeration bins into smart bins that monitor grain as it’s dried down.
The system’s sensor technology improves grain drying efficiency. By not having the means to thermostatically control their supplemental heating system, farmers have, in the past, often used too much heat, said Steve Rogoschewsky, owner of Adaptive Agriculture.
The two products utilize sensors that are placed between the bin fan and the air plenum to measure temperature, humidity and static pressure. With this data, they calculate grain drying time while accounting for fan size and speed. The Pro version allows a farmer to dry two bins simultaneously. Once the grain is completely dry, a process that takes three to four days on average, the grain-drying system can be removed.
The system hardware is paired with a web platform that allows farmers to track, monitor and save data related to individual bins as well as visually map their binyard and create a crop plan.
An additional aid to grain drying efficiency, Adaptive Agriculture’s Binstick is a portable probe used to monitor the drying process in loaded bins that are not equipped with sensor cables. The device can be connected to either Bindapt product.
Bindapt allows farmers to harvest grain earlier, said Rogoschewsky. “We’ve helped a lot of families across the Prairies to get through adverse weather for harvest, as well as expanding their tech to monitor the rest of their bins.
” It’s also more than a mere ad hoc solution, he added. “If you can get out into the field a week early, ahead of the ideal conditions for drying, you can start putting grain in the bin and dry it down. We’ve changed the way farmers view what their harvest picture looks like.”
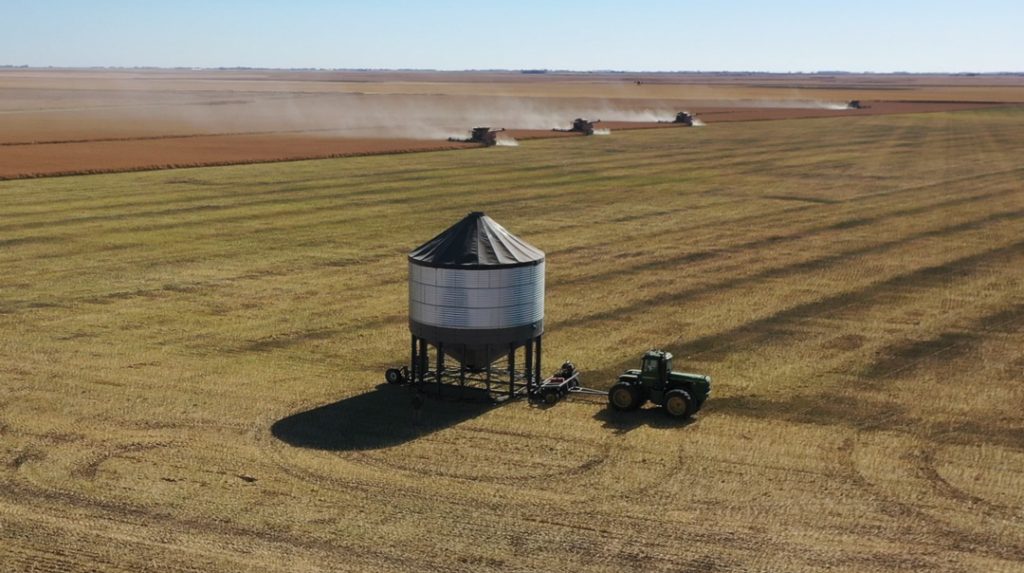
TELESCOPING MOBILE BIN HOLDS BIG BUSHELS
Not all farmers sell their grain straight off the combine. In times of harvest surge, many opt for temporary grain storage solutions such as grain bags. Certain farmers would rather not use grain bags, said Patrick Beaujot, one of three T-Bin AG Equipment business partners.
While plastic grain bags can hold as much as 8,000 bushels of grain, to fill them requires specialized equipment. Additionally, they are susceptible to the elements. Temperature and moisture can cause problems while insects and animals can also damage the stored grain, literally taking a bite out of profits. “Farmers love grain bags at harvest time because they can stick the grain in a bag quickly and move to the next field and keep combining, but they hate them after harvest when there’s a situation,” said Beaujot. “There’s always room for something better.”
Beaujot teamed up with engineer Trevor Phenix and Saskatchewan farmer Dave Kosior whose idea it was to create this grain storage option. The portable bin extends in height telescopically to increase capacity. Seventeen feet tall when collapsed, the T-Bin extends to a height of 36 feet and holds up to 10,000 bushels of grain.
The bin addresses several challenges. These include tight harvest windows and the chronic farm labour shortage. Farmers prefer equipment and systems that allow flexibility to spread out and grow. Many tend land far from their binyards, which makes hauling grain a tough and time-consuming gig at harvest. A temporary, moveable storage bin may be just what they need, said Beaujot. If needed, the bin can be equipped for aeration and remote monitoring.
The T-Bin comes equipped with a wheeled transport and lift kit that can be shared among multiple units and towed behind a tractor or semi truck. The unit can include an optional independent hydraulic unit that will support both telescoping and transportation lift requirements.
A notable nod to its value in the field, the T-Bin team earned the Farm Built Solutions Award at this year’s Manitoba Ag Days Innovation Showcase.
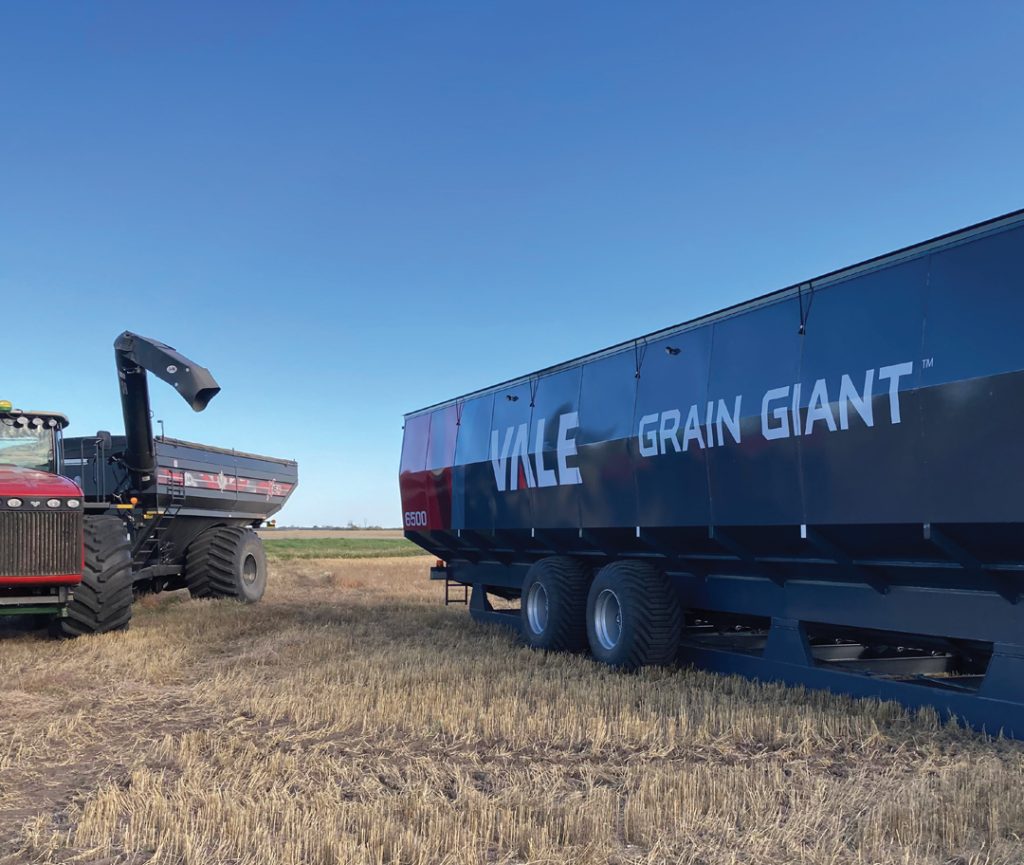
FIELD BIN A GIANT HELP
Over past decades, western Canadian farms have become larger and more sophisticated. Consolidation has created the need for bigger equipment and more employees. But no matter how big your combine is, you remain limited by the size of your workforce and trucking capacity, said Pieter Cruson, president and co-owner of Vale Industries at Indian Head, SK.
Large-scale Australian grain farmers have faced similar challenges. Their solution has been to invest in mobile field bins. Vale’s previous owner believed this type of equipment would serve western Canadian farmers well and so designed prototypes and built a manufacturing plant large enough to accommodate the project. Cruson and his wife Kendra purchased the company in 2020 and launched production of the Vale Grain Giant that same year.
The Grain Giant is designed to increase farm efficiency at harvest time. The mobile grain bin offers 6,500 bushels of field storage capacity that allows a farmer to operate at peak capacity while eliminating the immediate need for trucks to move the grain off the field.
“Typically the grain cart is desperately waiting for the truck and the truck is hustling to get back for the grain cart,” said Cruson. “With this in the mix, the grain cart always knows to dump into the field bin, and the truck always knows where to pick up.
It really reduces the stress level at harvest.”
The Grain Giant is hitched to a clevis on a tractor using a two-inch hitch pin. The discharge auger is raised and lowered with hydraulics, as is the draw bar, suspension cylinders and sweep auger.
At 22 inches in diameter, the Grain Giant’s discharge auger is quite large. It is PTO driven from the tractor and features an adjustable discharge spout powered by an electric actuator. During transport, the auger pivots and folds in.
The unit’s sweep auger runs lengthwise inside the bin and is controlled hydraulically from the tractor. The sweep auger dictates the amount of grain that enters the discharge auger.
It can be operated remotely from inside the transport truck.
The Grain Giant is also equipped with cameras, both on the discharge auger and at the rear. A camera mounted on the auger allows the operator to see inside the bin during loading. An additional camera acts as a rear-view mirror during transport that allows the operator to determine whether the grain door is open or closed.
Perhaps the most attractive feature is the remote control, which allows a farmer and trucker to load without additional labour. If the Grain Giant cannot be moved off the field at day’s end, its electric tarp secures the load against overnight precipitation.
When the Crusons launched production, they assumed the product would have the greatest appeal to farmers with especially large operations. As it turns out, the first units were sold to farms closer to 3,000 acres in size. “The reason these people were buying the unit is they just didn’t have the help,” said Cruson.
Alberta grain farmer Garth George calls his Grain Giant “head office.” George manages a 6,000-acre grain farm in Marwayne where grain is forward priced and sold right off the combine. This makes for a very stressful harvest, especially when truckers are in short supply. He was frustrated by the scarcity of available truckers and that he often had to pay them to sit around and wait for the grain cart to return.
George initially used the Grain Giant last fall. In his experience, production went up, while his stress level went down. He was able to cut costs because the new system kept truckers moving. “This machine might not be for everybody,” he said. “But on my farm, it was probably one of the greatest investments I’ve made in a long time.”
Comments