ADVENTURES IN CROP NUTRITION
BY TREVOR BACQUE • LEAD PHOTO COURTESY OF GENESIS FERTILIZERS/CATALYST REACTION
Fertilizer always has been and always will be vital to agriculture. However, this primary crop input has come under fire in recent years, most notably for its carbon footprint. The federal government took aim at fertilizer and its emissions, challenging industry to be more sustainable top to bottom. Price variability and unsteady availability of supply are also problematic.
Several companies have rolled up their sleeves to create Canadian solutions for an industry that remains hungry for plant nutrition products. Some are at work to create processes that will make production carbon neutral. Others upcyle abundant human waste as a potent source for fertilizer products. Many potential solutions to fertilizer problems are yet in development. All this activity suggests now is the time to examine new industry production standards in Canada and beyond.
If western Canadian agriculture had a heartbeat, it would be in Regina. Home to many major industry players, it only makes sense the country’s first low carbon nitrogen fertilizer plant would be located a stone’s throw from the Queen City at Belle Plaine.
The plant operates as a partnership between Saskatoon-based Genesis Fertilizers and South Korea’s Carbonco. The latter is a subsidiary of DL E&C, a Korean conglomerate also involved in the project. It has built hundreds of mega projects around the world, including the world’s longest suspension bridge. While Belle Plaine has a projected start date of 2029, many say it can’t come soon enough given the escalating cost of fertilizers.
The market volatility that began way back in the Great Financial Crisis of 2008 prompted Genesis CEO Jason Mann to ponder possible remedies. He realized long-term stability in price and availability was required for Prairie farmers. “This project is needed,” he said. “Farmers here are paying pretty much the highest price globally for nitrogen fertilizer, yet we produce the fertilizer right here and there is no logistics cost, other than [transport] from the plants in Western Canada to the farmer.”
The two biggest issues at hand for Prairie farmers are a limited number of suppliers and being landlocked. Because of this, they pay some of the highest rates, which in part is the result of massive freight costs. It’s why Mann is buoyant about a plant in the middle of the Prairies that will produce three unique products once operational.
The Belle Plaine facility will primarily produce granulated urea and granulated urea ammonium sulfate (UAS). It will produce 1,500 tonnes of ammonia per day, which will yield 2,500 tonnes of urea synthesis. In addition, the plant will also produce 250,000 metric tonnes of diesel exhaust fluid. With production slated to run 350 days per year, this translates to 1.1 million tonnes of total product. The plant can increase or decrease urea and UAS production depending on market demand.
Front-end engineering design has not yet been completed, but the total project price tag is expected to be just shy of $2 billion. To an extent, proponents see the final bill as a bargain no matter what the cost, given how cheap and plentiful natural gas, and to a lesser extent, water is, in Western Canada.
“The cost to make fertilizer is essentially your feed stock: natural gas, electricity, water and the cost to operate your plant,” said Mann. “The actual cost to produce nitrogen fertilizers is a fraction of what it sells for on the market.”
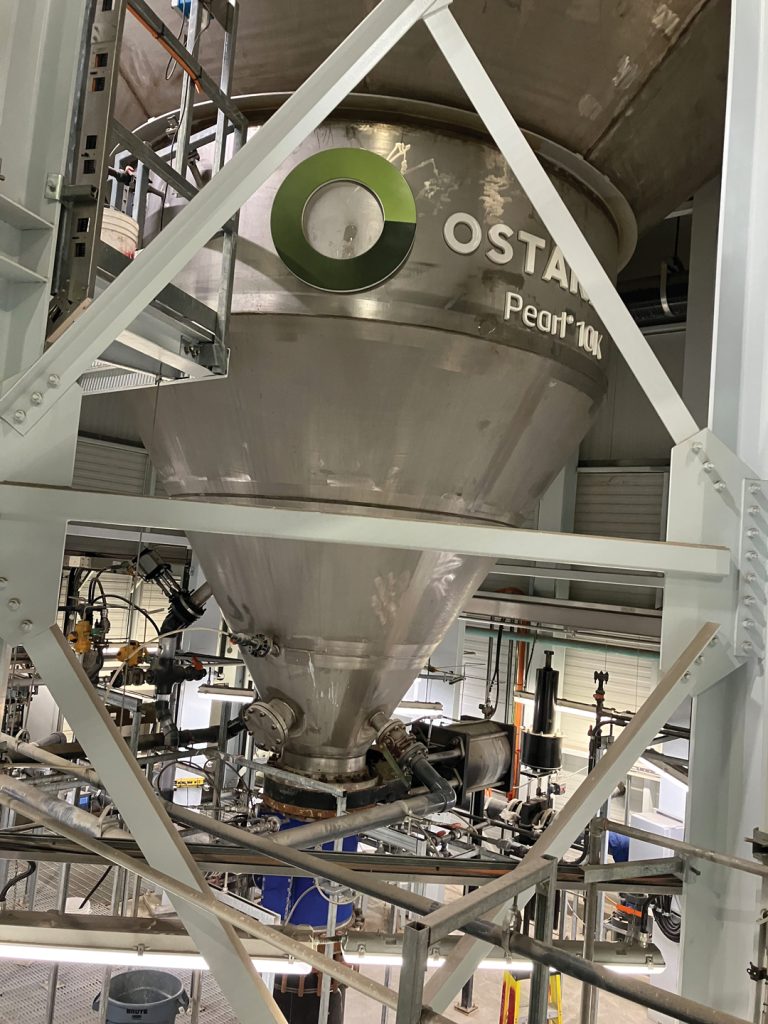
Triggered by world events, Canadian prices can skyrocket, as evidenced in 2022 with $1,300 per tonne urea thanks in part to Russia’s invasion of Ukraine. Mann wants to avoid exposure to such volatility. “Any incident like that can cause an upset in the market and cause a runup in price. Farmers have no control over that,” he said.
Each year, Canada produces about four million tonnes of urea. Nonetheless, the country imports about eight million tonnes, mostly from China, Eastern Europe, the Middle East and Russia. The Belle Plaine facility looks to flip the script to a degree.
CO2 emissions were an initially overlooked aspect of the plant’s operation. As designs unfolded, however, Mann and his team realized there was yet another opportunity for Genesis, but also farmers. “We’ve seen over the years a lot of pressure being put on farmers to reduce their carbon footprint and their GHG emissions in relation to nitrogen fertilizer,” he said.
At current estimates, Belle Plaine will sequester 700,000 tonnes of CO2 annually. With the price of carbon today being $80 per tonne, and rising to $170 by 2030, the math checks out. The plant’s carbon capture and sequestration model will be slightly different than the initial industry methods. At Belle
Plaine, CO2 will be captured, dehydrated and compressed into a liquid. It will then be sent down into the Deadwood Formation, a saline aquifer. This geological formation provides the ideal environment for long-term sequestration, as it allows the CO2 to bind with the porous rock, where it is securely and permanently stored. Western Canada is one of a handful of regions on earth with such formations able to safely sequester large volumes of CO2 over geological timescales.
“We’re solving a piece of that [reduction], because in our production, we’re capturing a lot of the CO2 and sequestering it, whereas other urea facilities are just exhausting that,” said Mann. “With a lower CO2 footprint, farmers will be able to use that in their calculation on their carbon footprint.
The trickle down to that is if you’ve got low carbon fertilizer, you then have low carbon grain, and we know there are companies out there today that are paying a premium for low carbon grain so they can meet some ESG targets of their own for their downstream customers.” Farmers who use low carbon fertilizer have a competitive edge against global peers, he said.
“This is an important project for western Canadian farmers so they’re not vulnerable to the market.” Nitrogen fertilizer demand will not shrink either, he added. “You may cut corners on some other nutrients, but you need your nitrogen.”
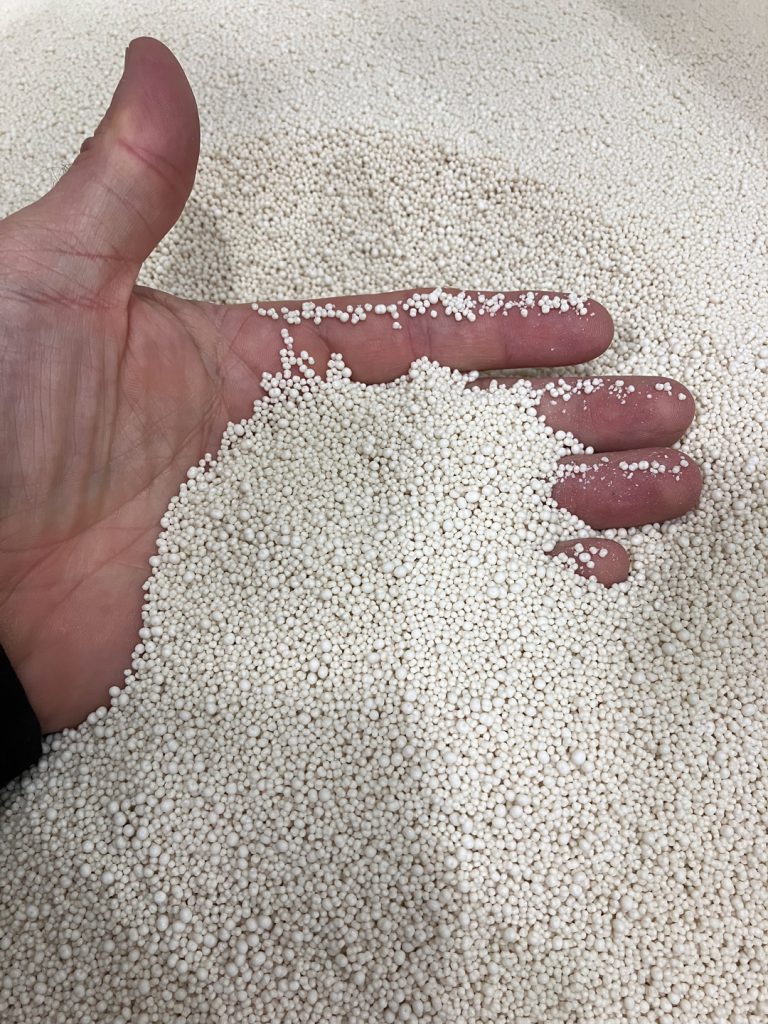
EVERY LITTLE BIT COUNTS
The City of Winnipeg has teamed up with fertilizer producer Ostara to build a nutrient recovery facility that turns human waste into slow-release phosphorus-based fertilizer. It will be ready to begin operations by 2030. What is primarily captured is phosphorus, which will be turned into a struvite-based fertilizer that contains phosphorus, nitrogen and magnesium and marketed through Ostara’s Crystal Green brand. According to the company, a farmer may be able to reduce their P2O5 application by as much as 50 per cent if conditions are favourable. Many tout the benefits of slow-release phosphorus, which is said to remain plant-available for multiple years once applied to a field. With facilities also operational in Saskatoon and Edmonton, Ostara makes good use of multiple cities’ waste. Globally, it operates more than 20 facilities that turn waste into fertilizer. Though each may produce a relatively small amount of fertilizer, in the aggregate, product volume and environmental stewardship are substantial.
In Edmonton, Epcor operates the Clover Bar facility, which has produced fertilizer since 2018. The plant receives digested sludge from the City’s wastewater treatment operation fed by five retention lagoons. Supernatant, the liquid that remains on top after solids have settled, is skimmed off and then fed into the facility’s reactor. Once inside, through a proprietary process, fertilizer granules are grown. Annually, this produces between 500 and 600 tonnes of fertilizer, which Ostara then sells as a phosphorus-rich product with a 5-28-0 rating. Ratios of its additional products may slightly vary.
“With this plant, any way you can take a waste stream and make it into a product that’s useable, that’s beneficial to the environment,” said Jeremy Barrett, the plant’s process risk and integration manager.
The reactor produces about 100 tonnes of Crystal Green each month between June and November. During operation, the reactor is fed 3.5 million litres of supernatant per day. As the plant removes phosphorus from the waste, it also reduces struvite buildup in the facility’s pipes, which, if bad enough, can severely restrict flow or block them altogether. Beyond that, the sequestration helps protect the North Saskatchewan River by increasing removal of phosphorus, which can cause algae blooms.
“The less phosphorus that we can have come back to the plant the better,” said Barrett. “Anything that you are treating less of, you’ll get a higher product going out. It’s a waste stream that we can make good out of. It can only benefit.” The facility is run on a cost-recovery basis. Profit earned from Crystal Green production is invested back into the operation of the plant.
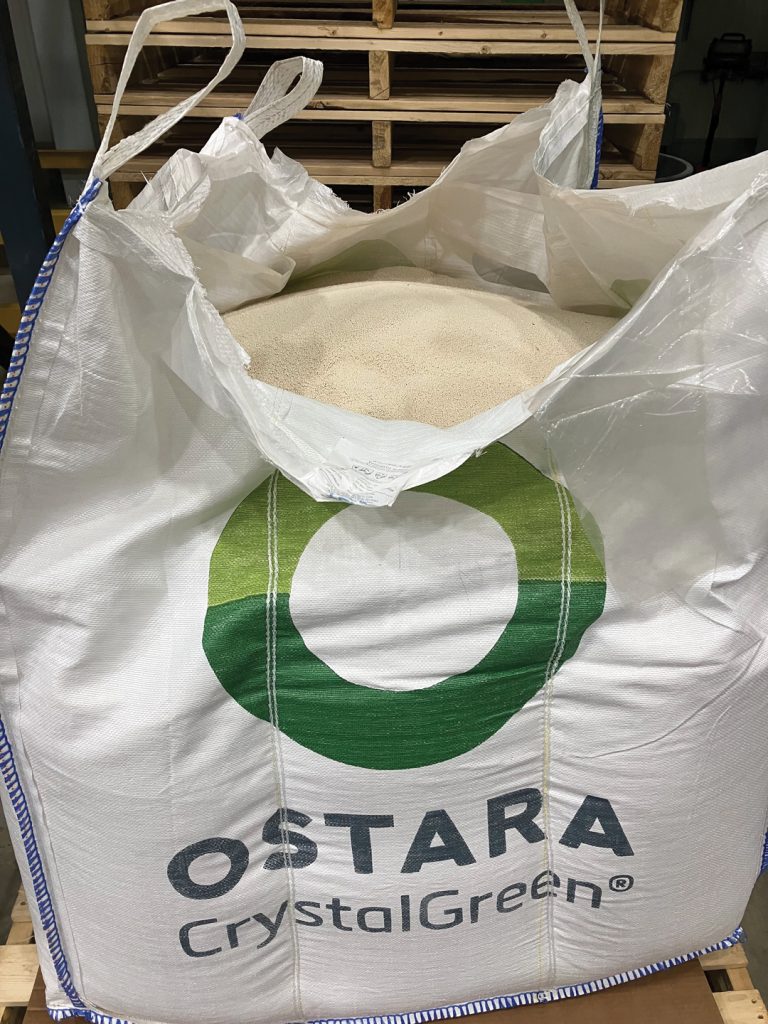
EASTERN PROMISES
The small French speaking enclave of Hearst, ON, is surrounded by a vast expanse of forest. It’s no surprise it once bore the designation as the official Forest Capital of Canada. If Stephen Case has his way, it may one day become synonymous with mining. Case is the CEO of Fox River
Resources Corporation, which holds the surface and mining leases to one of the cleanest, undeveloped phosphate rock deposits in North America. The goal is to give Canada a big push to gain a level of self-sufficiency through Fox River’s Martison Phosphate Project, a vertically integrated mining and fertilizer complex located 70 kilometres north of Hearst.
While it’s not clear how much phosphate rock is in the ground, Case believes it will be able to supply Canadian farmers’ needs for 25-plus years.
While municipal facilities may produce modest amounts of phosphate products, Martison’s resources would dramatically reduce Canada’s dependence on its importation of the vital nutrient, which now sits at two million tonnes per year, double what it was in 2010. When fully operational, Martison is expected to produce more than 940,000 tonnes of phosphate fertilizer annually in MAP, NPS and SPA formats.
Its current phosphoric acid plant design capacity is 500,000 tonnes of P2O5. Globally, estimates peg phosphate production at about 80 million tonnes each year, with China responsible for close to 40 per cent of that figure. Canada, by contrast, produces nothing. When Nutrien morphed production away from phosphoric acid to ammonium sulphate, so went Canada’s only source of production. Now, the country imports about 80 per cent of all its phosphate from the Americans annually with the remainder coming from Morocco. Canada stopped importing Russian phosphate following its invasion of Ukraine.
“The primary problem with all this is we’ve been relying on the U.S. for the last 40 years and their production is declining,” said Case. While he concedes the project is five to seven years away from being operational, it’s vital to press the issue today. The Hearst leases are rich in phosphorus, yet low in the heavy metal cadmium, because the rock is igneous, not sedimentary. “The beauty of Martison is it’s the highest grade undeveloped phosphate deposit with scale in North America,” he said. “The quality of it allows you to make all sorts of value-added products.”
Agriculture is the primary hand tugging the rope of phosphate supply, however, it’s not the only one. The development may also produce PPA, which is essential for lithium ion phosphate batteries. Today, demand exists for EV batteries, renewable diesel, ethanol and SAF, or sustainable aviation fuel. “If you are now growing more crops to feed your renewable diesel industry and eventually your SAF, that’s going to require more fertilizer because you need more crops,” he said.
Should the U.S. phosphate market dry up, Canada will have to call on other global suppliers. This would leave the country subject to supply risk and higher rates as a price taker. “You can’t rely on Russia or China because they’re non-allied to Canada and the U.S., and are responsible for over 45 per cent of the global phosphate fertilizer production,” said Case. “And both have already shown their ability to restrict their exports. You can rely on Morocco except that they’re in an unstable part of the world. So, what are we going to do; run from one supply risk to the other?”
He felt it was a problem in 2021, which prompted him to lobby the federal government to add phosphorus to Canada’s Critical Minerals List. Response was lukewarm. “They came back and essentially said, ‘You know, we get it from the States; we don’t worry about that,’” explained Case. “They just assumed because they got it from them for the last 40 years that it would just continue to happen, and that’s not the case.
That’s the problem.” Earlier this year in June, however, Case was part of a successful lobby to have phosphate designated one of three additions to the government’s Critical Minerals List: high-purity iron, silicon metal and phosphorus. It’s the kind of distinction that gives a real tailwind to push Martison forward.
Case works closely with neighbouring Constance Lake First Nation (CLFN) and has contracted community leaders numerous times on exploration assignments. “We have had a 20-plus year relationship with CLFN and have entered into various exploration and service agreements that involve employment, training, contracts and community support,” he said. “The Indigenous communities are an integral part of the success of this project, or any project in northern Ontario and Canada.
“I’m agnostic as to how it gets done,” he added. “It’s more important for me that it gets done and that all the stakeholders involved in that process are treated fairly. We have a two-million-tonne market today, and its supply is being jeopardized. So, you need to do something. It doesn’t have to be any more complicated than that.” Once operational, the project’s primary markets would be Ontario, the Prairies and the U.S. Midwest.
Comments