STUDY EXAMINES FUEL EFFICIENCY AND TAX REDUCTION
BY IAN DOIG • ABOVE PHOTO BY ANTHONY HOULE
A three-year Team Alberta study on grain conditioning has just produced its second-year results. To be completed in spring of 2022, the research project will assess the efficiency of various grain drying systems used by a selection of Alberta farmers. Initially inspired by the potential impact of federal carbon taxation, it will also analyze how various methods and fuel types can diminish the bite it takes from the farm bottom line.
With funding provided by the Canadian Agricultural Partnership, the Alberta Wheat and Barley Commissions have partnered on the project with the Alberta Canola Producers Commission and the Alberta Pulse Growers Commission. The Prairie Agricultural Machinery Institute (PAMI) continues to provide assistance with the project. GrainsWest spoke with Lorne Grieger, PAMI business development representative, Manitoba operations, about the study’s latest interim results.
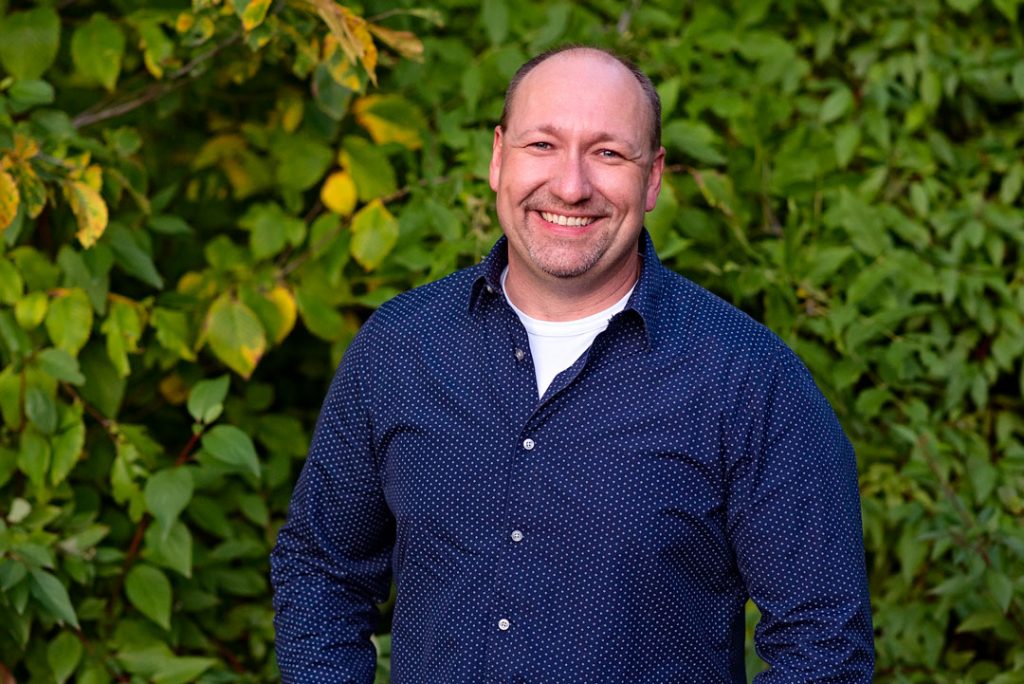
GrainsWest: What is the intent of Team Alberta’s three-year grain drying and conditioning study?
Lorne Grieger: The desire was to understand what the energy consumption is on farms for grain drying in Alberta. There is a lot of information from years ago, but there isn’t a lot on the state of systems currently operated on farms. One of the biggest gaps was systems used in-bin—natural air drying and supplemental heating. That was a big part of understanding the levels of energy consumption. With that, you can understand changes and implications for farmers that come with the carbon tax. That allows you to make adjustments and look for ways to make operational changes.
GW: How has the study progressed since its first year?
LG: There’s a lot of variability each year in agriculture. In on-farm research, you don’t get all the information the first time. A multi-year project allows us to fill in the gaps and understand the things we observed last year in greater detail. It also allows us to dig deeper into the initial findings to understand them better and to introduce additional constraints and areas to be studied. Three years helps you define that long-term potential.
GW: The first year of the study showed a surprising amount of variability among the drying systems studied. The efficiency of systems that use indirect heating was also higher than expected. Has year two thrown more light on these aspects?
LG: It has helped, and that’s where the additional data points come in. Why did we see the result we did in year one? Going back a second year allows us to zero in on this a bit more. Fall 2019 was particularly challenging for producers. The environmental conditions during that fall play into the results of this project. Having additional data points helps reduce that variability. We did see less variability as a whole in grain that was dried in 2020 compared to 2019. The more data points you have, the more confident you can be in the result.
GW: Have there been any surprises in the operational end of the second-year data?
LG: A couple of things stood out. We looked at a couple aspects of in-bin systems, one being a producer who had a rooftop-mounted ventilation fan to extract the moist air out of the top of the grain bin. When you’re drying the grain, you’re pushing the air from the bottom of the bin to the top, so that’s where moisture will accumulate. The majority of bins have a vent that the air flows out. We saw a difference with that particular setup in increased overall efficiency. This is the first chance we’ve had to get some data on this type of system. It’s really good to have this particular setup in the study.
GW: Carbon taxation spurred the launch of this study. What do the second-year findings have to say about this part of the conditioning equation?
LG: There is going to be an impact on producers who are drying grain. You require energy to be put into grain drying systems regardless of the fuel type. That’s going to impact the bottom line. It’s important to understand the different types of fuels and how that impacts the overall complement of energy types being consumed as well as the financial implications. And we’ve got potential changes that could be made either in the equipment setup or in policy to help producers manage or navigate an environment where you are providing the commodity at a price.
It will help at both ends I believe. And that’s an important thing to understand for the study: what’s that baseline? What is it costing producers on an annual basis to dry their grain? We want to make sure we’re competitive in how we do our crop production on the Prairies.
GW: The second-year report includeS policy suggestions that combine reduced grain drying cost with reduced greenhouse gas emissions. What do these most notably include?
LG: One aspect is efficiency. In what ways can you operate your equipment more efficiently and make adjustments in your equipment complement? The other aspect on the carbon tax side is the fuel type. Not every fuel type is taxed the same way. In overall economic impact, looking at switching to natural gas where possible, because it has lower greenhouse gas impact and it’s a better option in terms of cost. But not everyone will be able to connect. So, to be able to have access to systems that have a lower greenhouse gas component but also better economic potential and having good natural gas infrastructure to supply that is something to be considered.
GW: How will the taxation findings generated by the study be useful to farmers?
LG: It’s really important to understand what the increase in taxation level is going to mean down the road. What can occur in order to reduce the expense? It’s a combination, potentially, of capital investments but also operating methods that can reduce the overall energy consumption, improve efficiency and reduce overall taxation.
GW: What will the final year of the study entail?
LG: The third year is going to be a continuation of some of the things we studied the first year. We’ll bring in more data to understand that three-year average. We discovered some things in year two that we can dive into as part of our third year, providing greater information to producers in order to make decisions on setting up their systems and operating grain drying on their farms. This year, for example, one of our participating producers looked at optimizing his burner. The efficiency gain was notable. We can look into the potential of this for other producers.
Comments