BIN YARD BUILDOUT
BY TREVOR BACQUE • PHOTOS BY CREW6 PHOTOGRAPHY
Farmers love simplicity. The impulse to eliminate complication drives them to innovate and create solutions to various farm problems. As farms have grown larger and advancements in plant genetics have increased yields, progressively greater crop hauls have made on-farm grain handling more complex.
And where should this grain be stored? After all, farmers don’t want to be off-the-combine price takers. They have few options, one of which is turning their farmyard into a miniature grain terminal. On-farm grain handling, storage and drying solutions have continued their meteoric rise across many parts of the Prairies and for good reason—they protect the farmer’s crops, which is to say, their livelihood.
Perry Rumpf farms just west of Battleford, SK, alongside his father Henry and brothers Alan and Mark. Part of the family’s farm transition, which just concluded, was the creation of a long overdue handling, storage and drying setup.
Their setup has been designed specifically to clean pulses destined for export to Bangladesh and other parts of the Asia-Pacific marketplace. For a number of years, the Rumpfs had 350,000 bushels of storage capacity. The capability of the handling system was about 100 MT per hour and it took about 30 minutes to unload a super-B, which Rumpf described as “not terrible.”
However, as the family expanded the farm and increased yields, it became apparent change was needed. A plan was hatched to push overall capacity to 750,000 bushels of storage. They now have added 260,000 of their planned 400,000-bushel expansion, most recently in the form of three 20,000-bushel hopper bottom bins, and more were being built during the summer. They also have six 64,000-bushel bins in the yard.
Today, when trucks unload, they quickly dump into a 5,600-bushel surge hopper bin, which is constantly moving at 100 MT/hr. A super-B coming into the yard can unload and be gone within five to six minutes; not terrible.
Everything is now much more automated. A distributor head and foot pedal system allow an operator to swing a centralized bucket elevator to wherever Rumpf requires, whether to their NECO 24240 mixed flow dryer or final storage. Overall, the handling system moves 700 MT each hour. The brothers agree it’s pointless to take turns dragging the auger around the yard, wasting precious time.

“It makes sense for our operation to do away with grain augers,” said Rumpf. “That’s why we looked at the automated system. We can leave it to run, nobody babysitting, frees up a truck driver or wherever you need an extra guy.”
The Rumpfs run four Claas combines and a good day spent harvesting will see them bring about 750 MT back to the yard.
Their setup is also designed to ship out efficiently. When contracted grain needs to move, it’s pre-loaded into two overhead bins. “When it’s time to ship grain out and move it, it’s not a big deal,” he said. “We’d have the bin loaded overhead. We can load two super-Bs and the trucks are leaving the yard within 15 minutes. We’re spoiled.”
Along with more bins, the Rumpfs added that NECO dryer this past year. With 60,000 bushels of wet bin storage ahead of the dryer, the dryer runs all day with steady loads of grain to dry down. On average, it handles 1,800 bushels per hour of CWRS going from 17 per cent moisture to dry.
Overnight, the dryer’s addition changed the Rumpfs’ basic harvest planning process. “Last year, we didn’t have to stop or wait,” he said. “When we were done combining, I only dried an extra half day then the drying was all done and put away. We don’t have to move the grain, put it through the dryer—it’s tied into the handling system, then it’s done for the season.
“Our previous dryer, we had the attitude: ‘don’t use it if we don’t have to.’ Now we have the attitude: ‘we will use it every year and it’s cheaper.’”
They also straight cut their malt barley in late August, drying it from 19 per cent down to 13.5 per cent. “Basically, it buys you some days. You’re not waiting for it to come in naturally on its own. You get acres covered in a short period of time,” he said.
Given their 2020 harvest was free of logistical headaches, it was clear there’s no looking back. “It took a lot of stress off a person’s mind,” he said. “You just felt like you were ahead of the game and not being pushed, just actually enjoying it. We didn’t run late hours, we ran till 10:30 and shut it down. No matter how you look at it you are ahead of the game.”
WHAT THE FARMERS WANT
This kind of success story is nothing new for Ralph Wegman. As the CEO of Corr Grain Systems in Regina, SK, he has watched farm consolidation really heat up over the last 10 to 15 years and realizes that once you reach a certain land base, you need the handling solutions to accompany it.
“We’ve been trending towards larger farms for the last 20 years and what we are seeing, as customers grow in farm size, is the need for them to be able to harvest their grain and put it into a larger storage unit so they’re not constantly relocating augers and moving from smaller bins to smaller bins,” he said. “There’s a need for larger storage and handling solutions.”
He said the calls he gets these days are not for individual components, but entirely integrated systems to replace piecemeal setups. “We are seeing greater interest in developing more complex grain handling systems at the farmgate,” said Wegman. “Farm labour is a challenge alright; the more efficiencies you can build into your grain handling systems, to help them manage through the tighter labour force in the farm sector, the better.”
Many farmers, Wegman said, are very interested in elevated leg-and-drag systems that operate at a 7,500 to 20,000 bu/hr capacity. He said the most common capacity requested is 7,500 to 10,000 and it’s rare people want less than 7,500 for any setup.
The most common bin order is for 30,000-bushel units with flat bottoms. As well, there is increasing interest in 75,000- and 100,000-bushel bins. These bins often come in pairs, and a farmer typically adds two each year for a number of years depending on their storage goals.
Wegman encourages farmers to begin their homework immediately following harvest as he labels the entire process of upgrading the handling and storage systems to be a one-year project. “It’s become accepted in the industry that when you’re looking at investing multi-millions of dollars into a handling system, they take time to design and ensure that a customer has got the right details in their system,” he said. “Our experience is that they will start the process in the winter, with the expectation that we can get the product installed, ready to go for the upcoming harvest.”
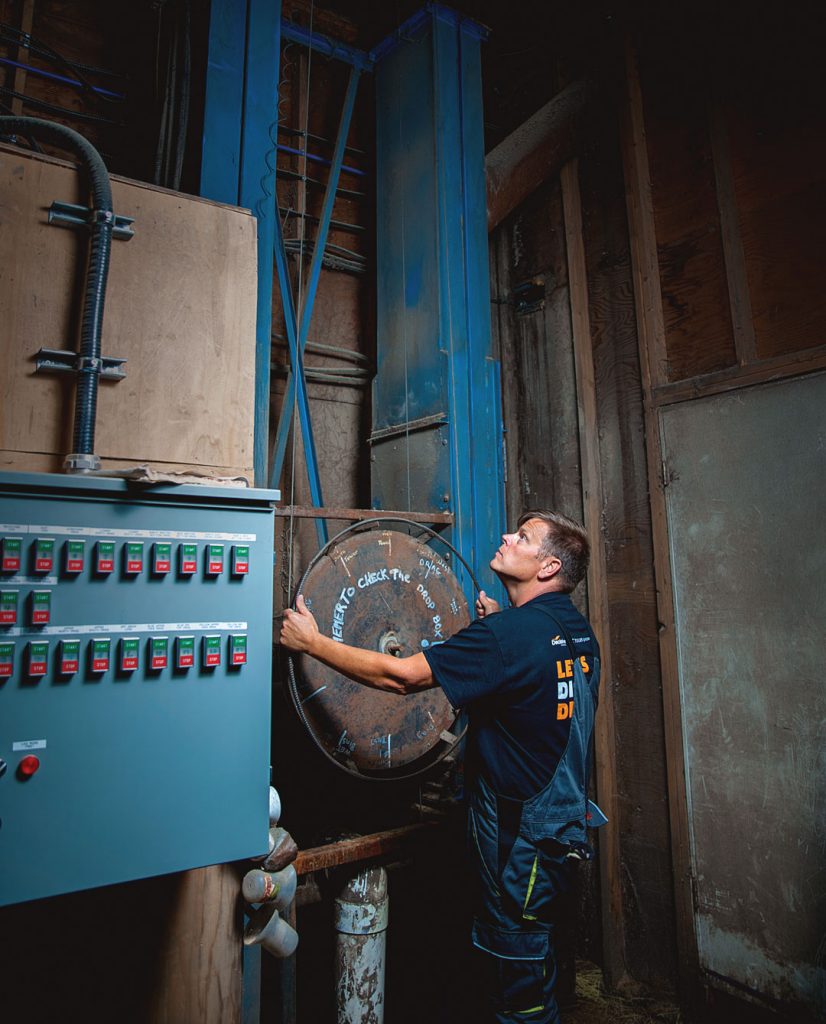
A farmer needs to consider the footprint of their farmyard or bin site and determine what’s possible and work from there. Also, consider the power and, if no three-phase has been trenched to the site, what that will cost. For the Rumpfs, their panel was upgraded from 400 amps to 1,200 to accommodate their new dryer. As well, the land itself must be properly designed and later prepped before any concrete can be placed. Any work a farmer can do ahead of time will save money on their overall bill. Future expansions should also be given consideration even though it may be years, or decades, down the road. If they are going to have an auger, Wegman also encourages farmers to determine the size needed. He said a 70-foot auger will work on a 25,000-bushel bin, but will be insufficient for a 30,000-bushel bin. Because a new auger may cost $100,000, this is something to consider as you pencil out the long-term amortization.
Blower systems are also increasingly popular. These work in tandem with a dryer, but not the initial handling of grain. A pneumatic blower sends the grain to different bins through six-inch aluminum piping. Grain is normally moved from a holding bin through the drying system and back into storage after the grain has been dried. This has a slower capacity of about 500 to 1,500 bushels per hour for handling grain from a drying system, but has the added benefits that, since it’s somewhat malleable, it zig-zags around a yard site above ground or underground with relative ease.
The systems work simply enough and most automatically adjust airflow settings to compensate for variable seed weight such as heavier wheat or lighter barley. Wegman said blowers are safe and unlikely to damage kernels, including pulses, which are generally more delicate.
The biggest benefit is that a blower system is a fraction of the cost compared to some more robust setups such as used by the Rumpf family. No one solution is “the right answer,” and Wegman said every farm site he deals with is unique. It ultimately comes down to what the farmer wants.
Wegman said the other segment, which represents less than five per cent of Prairie farms, is fully automated systems that resemble an inland terminal. Rather than utilizing a foot pedal and distributor head, every action is controlled from a computer terminal within an on-site shack. The only manual operation is the initial dump of the grain. Despite this being the smallest segment of the market, he expects it will grow, too, as farms increase in size.
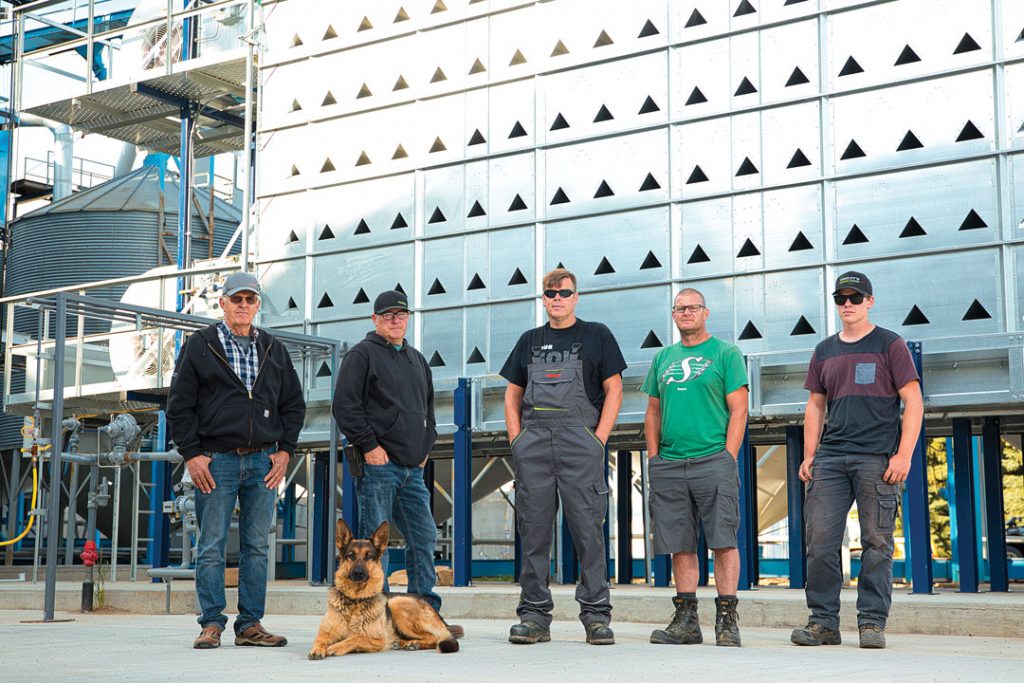
INDUSTRY RESEARCH
Much emphasis is placed on customization of handling, and it is equally important to sort out how grain will be monitored once binned for the season. It’s the primary focus for Jitendra Paliwal, associate dean in the faculty of Agricultural and Food Sciences and professor of engineering at the University of Manitoba. In addition, he leads research at the Canadian Wheat Board Centre for Grain Storage Research in Winnipeg, MB. The Centre is responsible for producing storage-related solutions that have been applied in Canada and around the world in countries such as China, India and Nigeria.
He said in Canada, farmers lose an estimated two to five per cent of their crop each year due to storage-related issues. “The focus is always on increasing the production when we could actually try and save or protect what we’ve already produced,” he said. “If you can make sure it doesn’t get spoiled, then you probably don’t have to focus on increasing so much on production.”
His research focuses specifically on post-harvest losses due to suboptimal storage. The answer? Constant and up-to-date monitoring.
One of the biggest success stories to come out of his lab was the technology that eventually became known as GrainViz. The system was born out of tumour detection research begun by Joe LeVetri at the University of Manitoba’s Electromagnetics Imaging Lab. Eventually, the technology was adapted to grain monitoring and later commercialized and ultimately sold to AGCO in 2020.
At the farm level, it is quite straightforward to use: A farmer installs the monitors, called transceivers, to the inside of a grain bin, turns them on and lets the units measure electrical permittivity of the grain. That is then used to generate a 3D moisture profile of the commodity, which can identify areas of high moisture, the primary precursor to spoilage.
“We know from experience, any time stored grain is getting spoiled, there are pockets of high moisture,” he said, adding he believes such technology is vastly superior to traditional cables. “With grain cables, it’s very localized measurements, no matter how many sensors you put on the cables. You can maybe get 10, 15, 20 per cent.” Paliwal said another big problem with cables is that if they stop transponding, there is no way to fix them.
This technology and others yet to be developed will prove critical to farmers who may store grain on-farm for nine-plus months. With major Canadian telecoms companies pushing into agriculture, Paliwal believes Canadian agriculture’s critical gap—a lack of connectivity—will finally start to disappear.
“That should have happened a decade ago,” he said of the push to connect rural Canada, specifically the Prairies. “We are hopping on that bandwagon a little too late, but better late than never.”
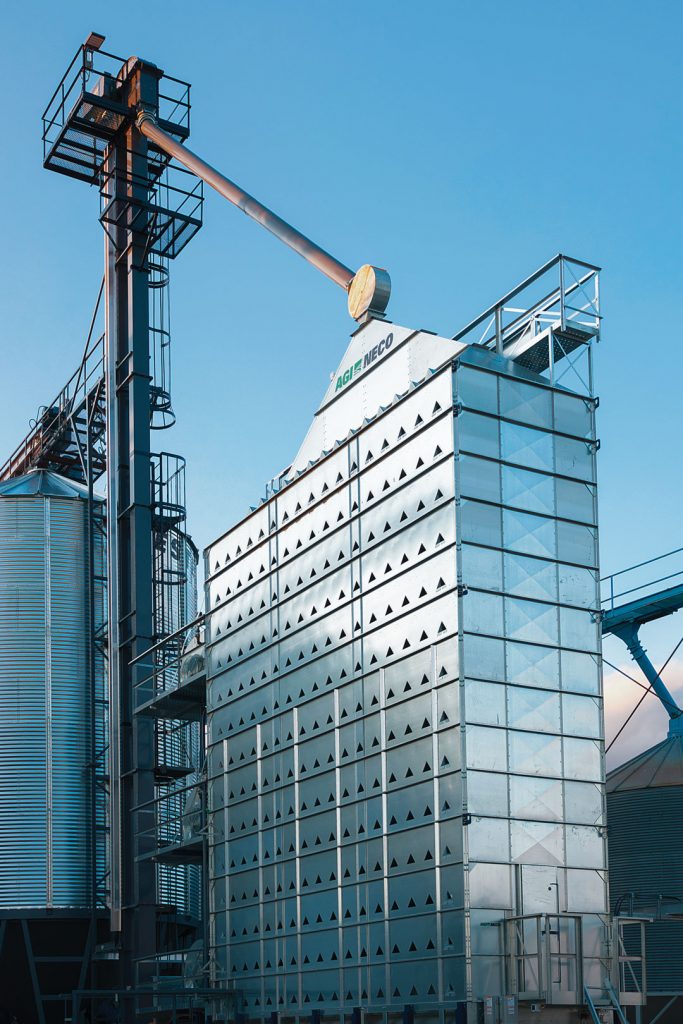
Paliwal sees a large-scale consolidation about to take place among monitoring providers simply because farmers “do not want to deal with 10 different apps for 10 different products from different vendors.”
Above all, he believes that the biggest challenge for farmers will be to invest in new technology when their current setup has still not paid for itself or is at the end of its lifecycle. “If you’re retrofitting, careful consideration has to be done to see what might be gained by spending that extra dollar,” he said. “If your equipment is done and you’re looking at putting in new infrastructure, the incremental cost of being rigged with sensors is not that great, so I’d say go for it.”
Back in Saskatchewan, Rumpf is loving life with his setup, but certainly knows the benefit of hindsight. He believes that if farmers are able, they should complete the process in one smooth motion and not piecemeal over a number of years.
“We pieced it together over 25 years, picked away at it, but when you do that it’s hard,” he said plainly. “That was our problem. Nobody thought we’d be where we are today and didn’t think bins would be as big as they are today. Do it in the beginning.”
Comments